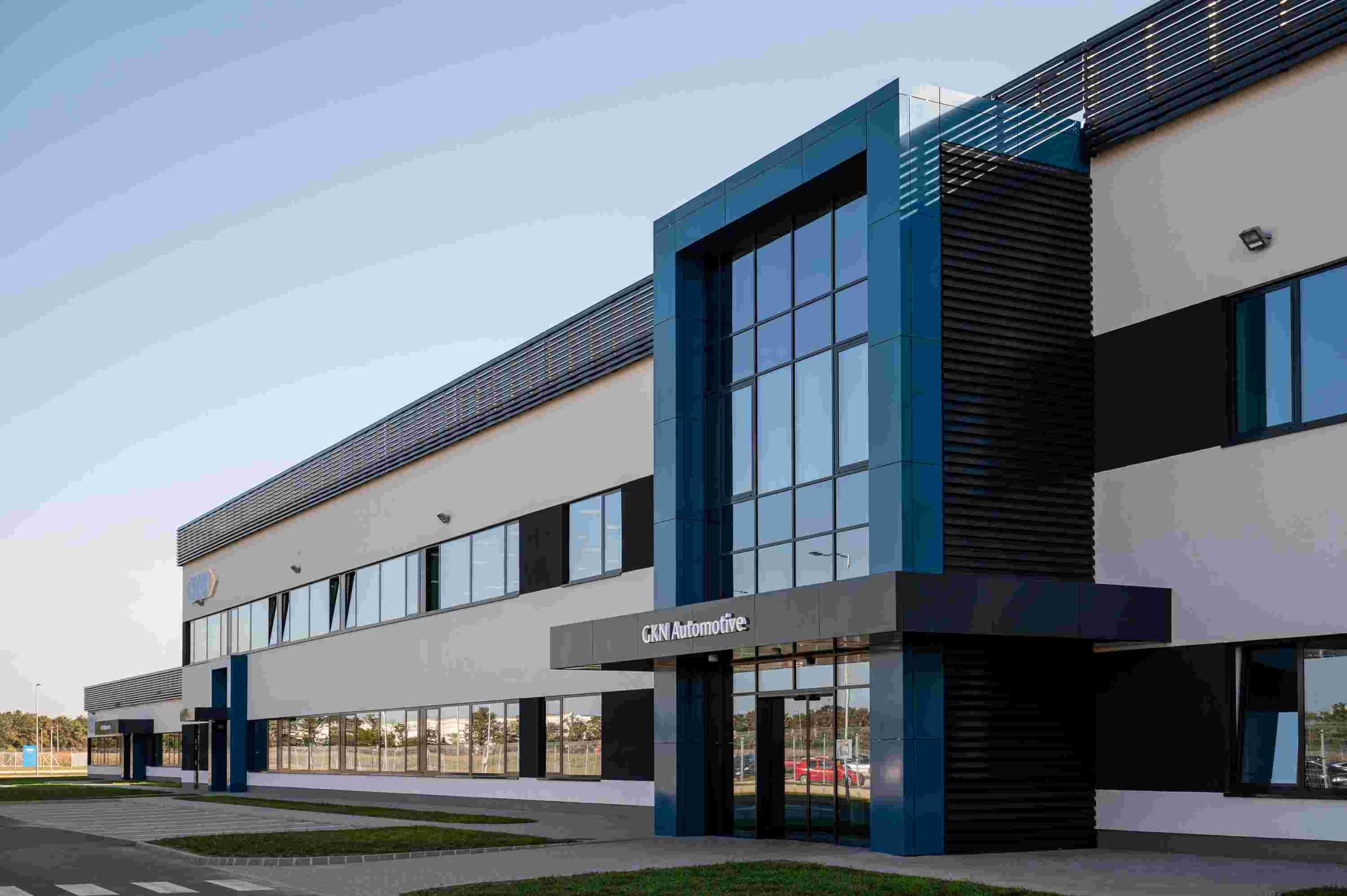
Tom Salisbury joined GKN Automotive a year ago in a newly created role as Director of Sustainability.
With more than 15 years of experience in sustainability teams across different sectors, Just Auto sat down with him to hear how he has settled in so far and what GKN Automotive is doing to deepen its commitment to sustainability strategies.
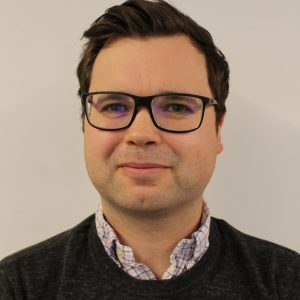
In your newly created role, what has been the biggest challenge you have faced so far regarding sustainability strategies for GKN Automotive?
When I joined, there was strategy in place and some great work was being done to define the main pillars of our strategy. It was really great to come into that context: where it wasn’t completely ‘starting from nothing’, and some really good work had already gone into that.
My challenge – and what my role here is to do – is to accelerate that work, and about making sure we have the strategy and targets in place, making sure we’re delivering [on that]. The Science Based Targets is a good example.
The broad challenge is the speed: there’s a lot to do in the context of sustainability and as a society. It’s one of these things where the goalposts are constantly moving, and making sure GKN Automotive is responding to that and continues to be on the front foot.
How well do you really know your competitors?
Access the most comprehensive Company Profiles on the market, powered by GlobalData. Save hours of research. Gain competitive edge.

Thank you!
Your download email will arrive shortly
Not ready to buy yet? Download a free sample
We are confident about the unique quality of our Company Profiles. However, we want you to make the most beneficial decision for your business, so we offer a free sample that you can download by submitting the below form
By GlobalDataIt [sustainability] is continually evolving and we have to ensure we are meeting the expectations of society and our customers.
“The broad challenge is the speed: there’s a lot to do in the context of sustainability and as a society.”
What does your day-to-day look like?
I spend time in the London office with my colleagues, but our executive team is dotted around Europe. Every quarter I have a sustainability update with them. In my first year, I’ve managed to get out to a lot of our sites around the world, and really look at how the strategy is being implemented out there as well.
Could you dig down more on GKN Automotive’s stragety for Net Zero – what are the different elements? What are the most important levers?
Our main headline target is Net Zero by 2045 in terms of our Scope One and Two emissions. For our direct emissions, the real lever there will be for us to move to purchasing renewable energy, so we’re actively looking at a PPA (power purchasing agreement).
In short, a PPA is a way you purchase renewable energy which adds renewable capacity to the grid – so we’re investing in renewable products. We have a roadmap to increase the amount of renewable electricity we’re going to be purchasing – that’s going to be the biggest way we can reduce our direct carbon emissions.
Energy efficiency is also at the top of our pile and that’s a really a big focus for our teams: replacing and modernising equiment and making sure energy efficiency is part of that.
We have 50-odd factories around the world, so that’s a significant footprint. We are also looking at where we use gas – heating – both in terms of premises and some processes that require gas.
The emissions associated with the vehicles that our products are going into now is a key element when we were finalising our science-based targets and looking at what was possible. That transition to EVs will play a huge role in terms of the eDrive business, but also the fact more of our side-shafts were once agnostic in terms of ICE or EV vehicles. Increasingly they will be going into EVs the closer we get to 2045.
Another key element to reduce Scope Three emissions is in our supply chain – how we engage with our suppliers on decarbonisation and also looking at how we move to green steel. It’s about looking at the carbon footprint of the products we are buying as well and moving towards net zero there.
It’s a real cross-functional effort: you’ve got the operation of sites, the engineering teams looking at how we can reduce the carbon footprint of our actual products, manufacturing [teams] adding circularity, and then procurement playing a really important role in the type of energy we’re procuring but also engaging with our suppliers.
“We’re increasingly working with our customers on reducing our carbon footprint and looking at due dilligence and the supply chain – there’s real opportunity for further collaboration in the sector.”
Do you have any examples of a project GKN is working on currently that you’re excited about?
The work on renewables has been really great and also we’ve got on onsite renewables. In some of our sites in India and other areas of Asia, and in Italy we recently installed solar panels. What’s been really exciting is that it has been great to see engagement across the business: we’ve got a really engaged executive team who get the importance of this and also an employee base who do, too.
We’re also about to roll out some e-learning for all our employees [on sustainability] which has been a really good project. That’s been exciting as it’s not about me and the sustainability team: it’s something for the whole organisation, making that relevant for everyone who’s working for the business. That’s really important.
The Bruneck site [Italy] is an important eDrive site for us. From a green perspective, operationally, that site is the first to use 100% green electricity, and using a groundwater cooling system, as it’s up in the mountain.
In GKN Automotive’s first sustainability report, ‘Innovating for Change,’ in 2022, it was reported that 99% of waste was diverted from landfill due to the implementation of circular economy – could you give some examples of how this waste is given a new lease of life?
Firstly, the vast majority of our waste from our sites is scrap metal. In machining you have small fragments of steel which look like little springs. As part of the process, that scrap metal is recycled.
When we think about circularity, it’s the biggest area we are looking at: considering the circularity of the products we are producing, reducing the waste wherever possible.
For our aftermarket business in Carcastillo, Spain, we re-manufacture sideshafts and they’re sold for the aftermarket. We manufacture around 20,000 sideshafts a year. It’s a significant facility that helps save steel but also carbon emissions – meaning these sideshafts are given a new lease of life.
Drawing from your previous experience, is there anything else you would like to add?
It’s been a new sector for me and that has been really interesting.
I was previously in the global sustainability team for Vodafone and then before that at AB inBev [Anheuser-Busch InBev], a global beer company.
There are a lot of similarities in the meta challenges we’re facing as a planet, as well as social challenges. It’s about thinking as a business: what’s the role you can play? What positive impact can you have?
What’s very interesting coming into GKN Automotive is how the customer requirements and expectations are also growing. We’re increasingly working with our customers on reducing our carbon footprint and looking at due dilligence and the supply chain – there’s real opportunity for further collaboration in the sector.