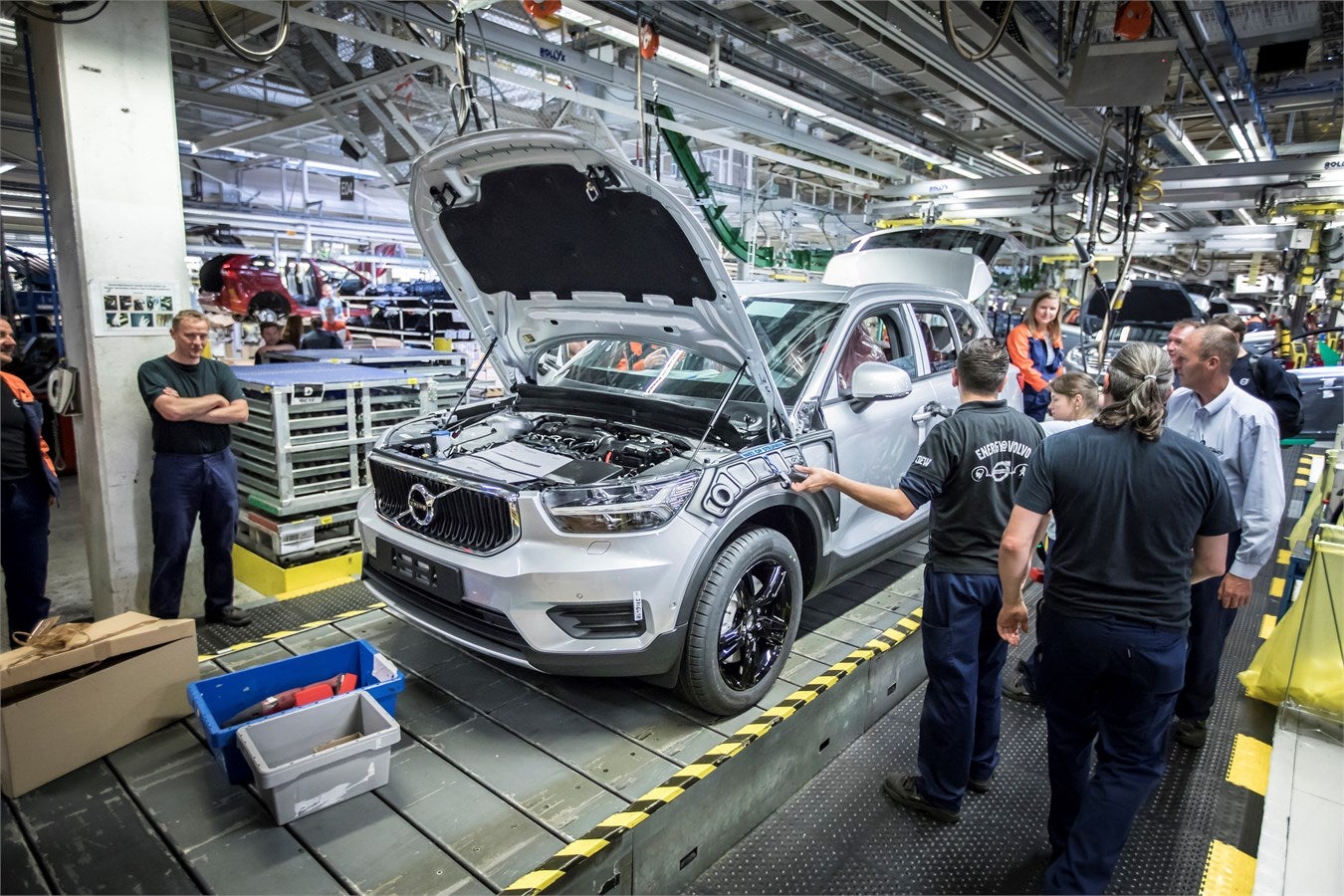
Critical Challenges Facing Automotive Supply Chains
A typical motor vehicle can contain anything between 15,000 and 25,000 component parts – depending on how they are measured and the design engineering of its major systems. That is a lot of material to bring together and provide integrity for the final product. Indeed, it is no mean feat to put all those parts together in the right order. Every car in existence is a tribute to process planning, organisation, production engineering and manufacturing logistics. Once upon a time, vehicle manufacturers were highly vertically integrated, but that approach gave way to divested (anyone recall where Visteon came from and the tangled web of companies that comprised General Motors’ Automotive Components Group?) and specialist parts suppliers who could focus on product development and operate more efficiently on higher scale to more than one customer.
The big Tier 1 systems integrators supply directly to the vehicle makers, often from supplier parks conveniently located close to vehicle assembly and manufacturing facilities, but there are multiple tiers of smaller suppliers below the top tier – each performing vital roles on the lengthy pathway from raw materials to the finished product.
How well do you really know your competitors?
Access the most comprehensive Company Profiles on the market, powered by GlobalData. Save hours of research. Gain competitive edge.

Thank you!
Your download email will arrive shortly
Not ready to buy yet? Download a free sample
We are confident about the unique quality of our Company Profiles. However, we want you to make the most beneficial decision for your business, so we offer a free sample that you can download by submitting the below form
By GlobalDataThe international sourcing of component parts has become an industry standard mode of operation over many decades as OEMs and larger suppliers have sought to shop around the global market for parts and material inputs that meet necessary quality thresholds at the lowest cost. Distances (and costs) for transportation and arrangements for warehousing are also a part of the picture, but higher efficiencies and technological advances in international freight shipping have underpinned phenomenal growth in international parts shipments.
The growth of the Chinese auto industry over the past two decades has also been a big factor in global sourcing of automotive components, especially what might be termed universal or commoditised parts that sell mainly on cost price. Chinese suppliers have benefited from big local contracts that boost scale economies as well as hidden subsidies that flow from complex ownership structures involving OEM parents, state enterprises and diversified stockholdings. In the early 2000s, the US vehicle makers, in particular, moved to source more low-cost parts from Asia, in the process undermining some long established companies in the US supplier base.
Across the globe, international trade flows in automotive products – both finished vehicles and component parts – are now huge. Estimates compiled by GlobalData show Germany as by far the world’s international leader in terms of outbound shipments of automotive industry products. Those exports are mirrored by imports and a tangled web of intermediate goods that are used as inputs to components systems that are refined and engineered at different stages of the manufacturing process and can be shipped across international borders multiple times.
A further important structural characteristic to supply chains in the auto industry is the importance of a supply chain management philosophy that minimises inventory costs and enhances process efficiency and feedback communication loops for enhanced quality standards. Known as ‘lean manufacturing’, it began with Toyota and its essence is encapsulated by the term ‘just-in-time’ to describe the lean supply methods and principles. The rise of digital and connected technologies that bring together all parts of the manufacturing and retail process have further underpinned these ways of working over the past decade or so.
In the past, natural disasters and their concentrated impacts on locations have impacted automotive companies and illustrated the fragility of automotive supply chains. After the 2011 earthquake and tsunami in Japan, there were several notable examples of disruption. A global premium car manufacturer had problems in terms of supply or a red paint pigment single sourced in Japan. Floods in Thailand later that year caused a shortage of supply of LCD screens for vehicle info displays. OEMs and dealers had to adjust to shortages accordingly. War in Ukraine illustrates how unexpected geopolitical events can disrupt supply chains, too.
The semiconductors challenge
All companies were adversely impacted directly by the public health crisis of 2020 and indirectly by many more effects on global supply chains. Moreover, the recovery to global sales in 2021 was severely impaired by an unforeseen consequence of the Covid crisis a year earlier. As vehicle makers shuttered factories under government orders and cut back drastically on orders for parts in 2020, the manufacturers of semiconductors found alternative business to be found in areas such as consumer electronics.
When recovering automotive plants stepped up their chips orders in the first quarter of 2021, a problem of tight supply rapidly became evident.
Semiconductor shortages were also not going to be easily overcome because of long lead times in adding chip foundry capacity upstream. An absent part that is safety critical or in some other way deemed necessary for the finished product meant that some model lines were more acutely impacted than others. Vehicle makers could shuffle the market mix in some cases, but an old adage was coming true again: Supply chains are only as good/robust as their weakest point.
Across the industry, procurement methods and processes are coming under scrutiny like never before.
It’s worth noting also that there is a structural element at work which means some semiconductor supply pressures are likely to remain a risk in the future: the advanced electronics content of vehicles is rising due to the ever-rising fitment of more sophisticated technological features. This is making some companies move to strategic alliances with chips makers. Not only can this help secure future supplies of critical microprocessors, but it can also facilitate beneficial collaborative future product development relationships in what is becoming obvious is a strategically valuable component area.
Other pressures on supply chains have come from other sources such as unforeseen labour shortages and much higher international container shipment prices as energy prices have spiked.
The dual- versus multi-sourcing debate
Fragility in automotive supply chains comes with the prevalence of multiple tiers, international sourcing flows and a tendency for single sourcing to maximise scale economies across global vehicle programmes. In many instances, this traditional structure is also embedded and ingrained in a culture of preferred partners across the supply tiers. Advantages can also include shared systems and logistics costs, with cost spread across volumes on other models and systems also.
Technology has also played a part in encouraging single sourcing as companies – including those in tiers 3 and 4 – have typically been able to centralise expertise and investment in one facility dedicated to high-volume manufacturing. The problems come when something goes wrong that scuppers plans (the fire at a Renesas microprocessors plant last year, for example).
Electronics and sensors are examples of critical components for sub-assemblies that can have big implications downstream in vehicle manufacturing if there is any disruption upstream. Finding alternative suppliers with spare capacity at very short notice is a big challenge.
Holding some reserves of parts in stocks comes with a cost and goes against the guiding principles of lean manufacturing. The decision can be taken, of course, to absorb or write-off any outlier disruption costs as and when they occur – it ultimately depends on the risk assessment quantification.
The experience of recent years does at least point to companies increasingly asking the question of whether singe-sourcing is as desirable as it once was. A world beset by higher risks and uncertainties perhaps demands a reset in approach. Duplication within the supply chain, even if it means getting close to sharing with a competitor, may offer a better solution – at least for some components – than single sourcing. Greater product security would be the benefit of dual sourcing. As ever, it’s a question of overall cost.
Electrification and new supply chain patterns
Electrification brings new challenges to future supply chains in automotive. The OEMs have faced considerable uncertainties over the supply of new and key components – most notably powertrain batteries – that they are trying to resolve. There are also strategic questions over the degree of vertical integration that is desirable to mitigate future risks and exercise control over the commercial aspects of supply arrangements. Joint ventures with battery specialists have been set up. Other key components for electric vehicles – such as motors, drive system parts, high voltage inverters – will also be subject to increasing investment alongside supply chain considerations.
Ambitious electrification strategies will see demand for lithium-ion battery cells skyrocket. Battery producers around the world are committing to multi-billion-dollar expansion strategies, opening new ‘gigafactories’ to supply cells to automakers.
One notable example of deep OEM-Tier 1 collaboration in this area is provided by the signing of an MoU between Volkswagen and Bosch. The two companies plan to supply integrated battery production systems, on-site ramp-up, and maintenance support for battery-cell and battery-systems manufacturers. The say they are aiming for cost and technology leadership in industrial-scale battery technology and the volume production of ‘sustainable, cutting-edge batteries’.
In Europe alone, the Volkswagen Group plans to build six cell factories by 2030 and other makers are taking similar steps to secure future supplies of cells and battery packs. The region should see a total annual battery pack capacity of around 700 gigawatt hours by 2030.
Looking upstream, Toyota has formed a JV with Panasonic (Prime Planet Energy & Solutions – PPES) that has signed an agreement with mining giant BHP for the future supply of nickel sulphate, the basis for the nickel present in the cathode of most lithium-ion battery cells. Tesla has also signed a similar agreement with BHP, illustrating that raw materials are also very much in the mix for future security of supply.
These deals highlight the need for automotive players to look further up the battery supply chain, to ensure they have access to sufficient raw materials to supply the enormous capacity growth needed within the lithium-ion battery sector for the new wave of battery EVs launching in the coming years. Recycling is also a key consideration in many of the deals that have been done.
Blockchain for supply chain visibility
Increasingly, automotive companies are utilising blockchain technology to gain transparency on supply chain issues such as CO2 emissions and the source of cobalt for batteries (which can come with ethical questions surrounding the mining of precious minerals).
The original blockchain concept, as the name suggests, is a chain of time-stamped blocks or records (block = digital information; chain = the public/community database). Blocks store information about transactions. When a block stores new data – a transaction – it is added to the blockchain and, once verified by a peer-to-peer network of computers, anyone can see it (or it may be subject to the permission of a private network such as an OEM’s supply chain – the ‘distributed ledger’).
However, all parties only have access to the information they have permission to see. Each computer in the blockchain network has its own copy of the blockchain. In principle though, the idea is to create a highly transparent system with zero transaction costs between the two parties creating a block.
We can expect to see more automotive companies adopting blockchain processes – especially of the distributed ledger (ie private network) type – as a means to mitigating the risk of supply chain ‘breaks’ and understanding strengths and weaknesses along the chain, but also as a way to demonstrate increasing demands for compliance in regulatory areas such as sustainability.
Lessons from Toyota
Toyota is generally viewed as one of the automotive industry’s better performers when it comes to supply chain management. As well as being the originator of the lean manufacturing methods which later became widespread best practice adopted by most OEMs and major suppliers, it has also refined its systems and processes according to changing circumstances regarding risk mitigation measures. Moreover, it has worked very closely with its suppliers at times and in the interests of broader sector aims in the face of emergencies.
After the Kyoto earthquake and tsunami of 2011, Toyota worked alongside suppliers in Japan to produce a comprehensive database of supply chain information to support Japan’s manufacturing sector. Toyota also introduced a strategy for multiple sourcing of key parts which would mean organising supply from three different sources – but with the main supplier geared to make almost two-thirds of the order to ensure scale economies. Multiple suppliers do compromise scale economies, but it does also mean that alternatives are in place if necessary.
Toyota also has a well-developed system in place to monitor its vast network of suppliers and an early-warning system for shortages. Indeed, some companies are turning to AI to assess developments in their supply chains – although that is predicated on possessing a reliable, extensive and detailed database in the first place.
Another option for companies is to embark on maintaining emergency or buffer stocks of key parts – particularly those that can cause a production line to stop. Again, it involves extra cost in storage or warehousing, but it’s a question of making a call on what level of cost or ‘insurance premium’ is worth paying. Also, it won’t be a permanent solution. Toyota may have stockpiled some semiconductors, but the severity of the global shortage of chips meant that, eventually, it too was forced to cut production. Perhaps the most significant learning from Toyota is a need for constant review and adaptability to changing circumstances and uncertainties.