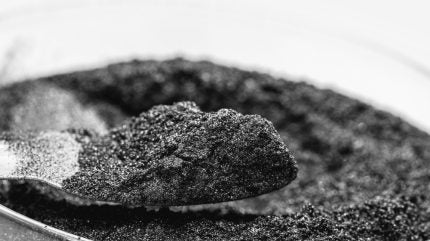
Over the past 10 years, advancements in the battery industry have enabled portable consumer electronics, the mobile internet, the first electric vehicles (EVs), and the initial adoption of intermittent renewable power storage and generation. As governments worldwide ramp up efforts towards decarbonising economies, demand for cost-effective, safe, high-performance, long-lasting, and low-carbon batteries will rise. The majority of this demand will come from the automotive industry.
According to GlobalData, the on-going, global build-out of new capacity in the pipeline means that by 2030, battery production will be sufficient to meet the world’s needs. However, attention is needed when it comes to the industry’s manufacturing processes. The production of battery materials can present numerous obstacles and, to overcome them, manufacturers must upgrade their facilities and production equipment to ensure they meet a range of standards and regulations.
The milling process in particular comes with its own set of unique challenges. Graphite, for example, is a vital component for lithium-ion batteries. However, milling it to nano-size for use in battery products is far from straightforward.
Graphite milling challenges
Providing great conductive properties, a relatively low-cost and the ability to cope well with the flow of lithium ions during charging and discharging, it’s no wonder that graphite is the most common choice of anode material in lithium-ion battery manufacturing. GlobalData analysis for the period 2022-2025 predicts production of graphite will increase from 1,145.5kt in 2022 to 1,567.2kt in 2025 – an 11% compound annual growth rate. (CAGR)
Due this soar in demand, manufacturers will be under pressure to ensure their manufacturing processes and equipment can rise to the challenge. Key to this will be the selection of good milling methods and machinery.
While the choice of milling methodology for graphite will depend on several factors such as the desired particle size, material characteristics, and the specific requirements of the formulation or process, current techniques include ball, hammer, pin, and disc mills.
As the handling and processing of hazardous materials such as graphite presents safety challenges for manufacturers such as loud noise levels, high process temperatures, and dust particles – all of which can be dangerous for operators – robust containment is crucial to preventing cross-contamination and exposure to workers and the environment.
Fire is another risk for operators during the graphite milling process. This risk increases significantly if the handling of the materials involved is carried out improperly. However, the implementation of protective measures such as good ventilation and fire detection and fire prevention systems can help to mitigate this hazard.
For millers, it is critical to comply with regulatory standards and quality control, to ensure safety, uniformity, reproducibility, and product quality. The utilisation of the latest technologies and high-quality equipment in collaboration with robust safety measures can help battery manufacturers to keep their employees safe.
Safety solutions
Frewitt is a world leader in powder size reduction technology and offers a range of innovative solutions and cutting-edge products for the sector. Based in Switzerland, Frewitt has long been at the forefront in the development of dry and wet milling processes, and its PowerMill PMV-320 revolutionises the process, improving not only fine milling efficiency and high performance but also enhanced safety for operators.
The PMV-320 is a single system that combines containment and micronization, and comes equipped with an automatic integrity test pre-operation to ensure a fully contained process. It operates under controlled vacuum conditions, eliminating the risk of explosion and protecting operators from exposure to toxic substances.
According to Antoine Virdis, Frewitt’s CEO-CTO: “The PMV-320 was conceived and designed to ensure that the customer is not obligated to make any compromises on user safety, product safety, usage ergonomics, efficient operation, productivity, and of course, on his Return on Investment.
“Safety is always our greatest priority. Working under a vacuum environment, processing with the PMV-320 takes place in a negative pressure. The removal of air deprives the environment of O2; hence combustion cannot take place. In addition, the negative pressure of the process keeps the product contained and is compatible with the most exigent OEB levels.
“Other milling processes have an interior atmospheric pressure considerably higher than the surrounding, ambient environment, and over pressures must constantly be guarded against. The PMV-320 is also ATEX 0/20 Interior certified.”
To find out more about Frewitt’s milling capabilities, download the whitepaper below.